Leading Metal Stamping Solutions for High-Quality and Cost-Effective Manufacturing
Leading Metal Stamping Solutions for High-Quality and Cost-Effective Manufacturing
Blog Article
Checking Out the Globe of Steel Stamping: From Design to Production
Within the realm of manufacturing, metal stamping sticks out as a specific and reliable method for forming metal sheets into various forms with amazing consistency. From the preliminary style phase where complex patterns materialize to the complex manufacturing procedures, metal stamping is a blend of creativity and engineering. Exploring this world unveils an intricate interplay of imagination and technical mastery, providing a peek into a realm where development meets craftsmanship.
History of Metal Stamping
Metal marking, an extensively made use of production process today, has a rich history that dates back to old times (Metal Stamping). The beginnings of steel stamping can be traced to old human beings such as the Egyptians, that utilized stamping methods to decorate jewelry and accessories with detailed styles. In time, metal marking progressed, with worlds like the Greeks and Romans using it for creating coins and decorative things
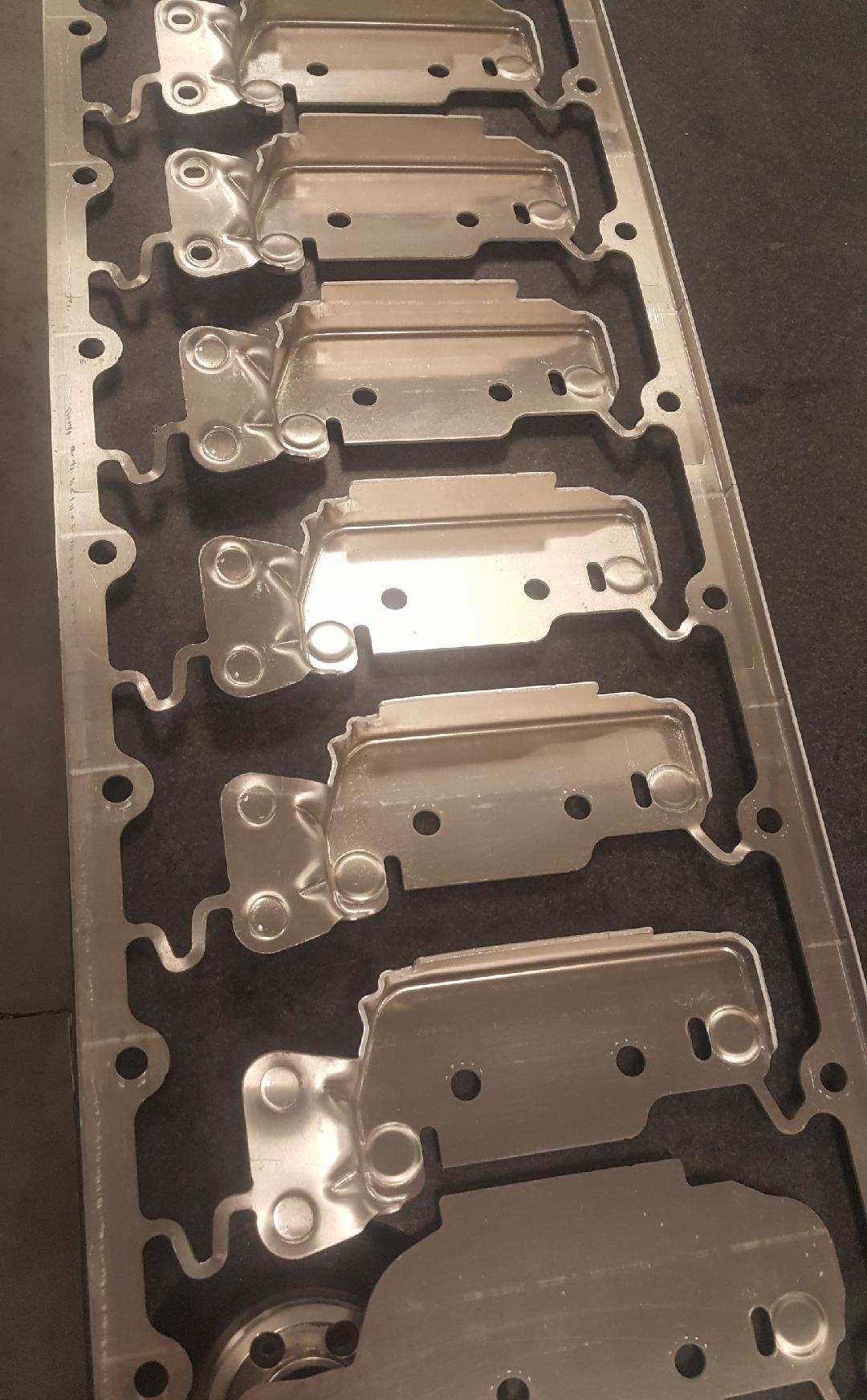
In the 20th century, metal marking remained to evolve with the assimilation of automation and computer mathematical control (CNC) technology. These innovations even more raised the effectiveness and accuracy of metal marking processes, making it a crucial part of modern-day manufacturing across sectors such as automobile, aerospace, and electronics. Today, steel stamping stays a crucial manufacturing procedure, incorporating tradition with advancement to meet the demands of a continuously advancing industry.
Style Factors To Consider and Prototyping
When developing metal marking tasks, precise interest to make considerations and prototyping is important for making certain optimal manufacturing results. Layout factors to consider in metal stamping include material choice, part geometry, tooling layout, and production expediency. Selecting the appropriate product is important as it affects the component's efficiency, price, and manufacturability. Component geometry influences the complexity of the stamping procedure and the capability of the end product. Tooling layout plays a significant role in the success of metal stamping projects, affecting component precision, tool durability, and production effectiveness.
Prototyping is a crucial phase in the metal marking procedure that enables engineers to evaluate the design, validate manufacturability, and make necessary changes prior to full-blown production. Prototyping helps recognize potential issues early on, conserving time and expenses in the future. It also gives a possibility to enhance the design for efficiency and top quality. By meticulously taking into consideration style aspects and making use of prototyping, makers can improve the metal marking process and attain high-quality, cost-efficient manufacturing outcomes.
Tooling and Devices Basics
Taking into consideration the important role that tooling style plays in the success of steel stamping jobs, recognizing the important devices and tools required is vital for accomplishing reliable manufacturing outcomes. Tooling is an essential facet click site of metal stamping, as it straight influences the quality and consistency of the end products. Important devices consist of passes away, punches, and fixtures, which are custom-designed to form and create the steel right into the desired parts. Passes away are the key device used to cut and develop the metal, while strikes aid develop holes or particular shapes. Fixtures hold the steel in area throughout the marking procedure, ensuring accuracy and repeatability. Additionally, tools such as marking presses, feeders, and coil handling systems are crucial for automating the marking process and raising performance. Buying top quality tooling and tools not just boosts production efficiency but likewise brings about greater precision, minimized waste, and total price financial savings in steel marking operations.
Production Refine and High Quality Control
Successfully managing the manufacturing procedure and executing durable top quality control procedures are important for making certain the success of metal stamping tasks. The manufacturing process you can look here in metal marking involves a series of steps that must be very carefully coordinated to achieve ideal outcomes.
Quality control in steel stamping is critical to deliver items that satisfy the needed specifications. By maintaining stringent quality control standards, suppliers can maintain their track Discover More Here record for delivering high-quality steel stamped items.
Applications and Market Insights
In the realm of metal marking, the effective application of manufacturing procedures and top quality control measures directly influences the efficiency and reliability of various industry applications and provides beneficial understandings right into the field's functional characteristics. In addition, steel marking assists in the manufacturing of different home home appliances, consisting of fridges, washing devices, and ovens, by offering cost-effective solutions for manufacturing sturdy and intricate components. Comprehending the applications and sector understandings of metal stamping is important for optimizing manufacturing procedures and improving product top quality throughout different sectors.

Final Thought
Layout considerations, prototyping, tooling, tools, production procedures, and quality control are crucial elements of steel stamping. With its prevalent applications and industry understandings, metal stamping proceeds to be a versatile and reliable manufacturing procedure.
Report this page